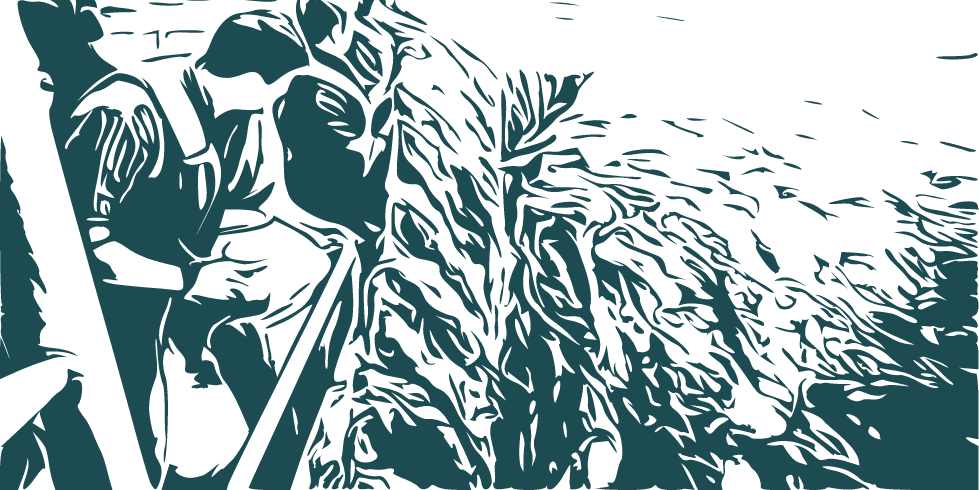
A field-validated method for predicting storm loads on open-ocean seaweed farms
Case Study Overview
Kelson Marine worked with the U.S. Naval Academy, the University of New England, and Callentis Consulting to develop a Validated Tool for predicting Hydrodynamic Loads on large open-ocean Macroalgae Farms, funded by the U.S. Department of Energy’s Advanced Research Projects Agency for Energy (ARPA-e).
Problem Statement
The hydrodynamics of flexible structures are complex. It is easy to significantly over-predict or under-predict structural requirements if you use overly simple estimates. So we need accurate, practical numerical modeling techniques to be able to efficiently design large seaweed farms for exposed sites.
Engineering Challenges
Low-trophic aquaculture with shellfish and macroalgae, or seaweed, can help feed the world and help restore the oceans at the same time. But working in the open ocean is difficult and expensive.
To realize this future, we need rigorous ocean engineering for offshore aquaculture.
We need to design for survival, but also to minimize crop loss in storms, to handle predators and avoid entangling endangered marine animals. We need to design for safe navigation and operations, and ultimately we need to be able to engineer these structures for maximum social, environmental, and economic sustainability.
Design Process Notes
Balancing all of those requirements is extremely difficult. But we can summarize the engineering process in three steps:
- Identify the requirements.
- Evaluate the system’s structural behavior.
- Then design, and optimize the economics.
To identify structural requirements, we start by quantifying the expected extreme wind, wave, and current conditions. We gather historical data for the site and identify extreme events. We then fit those data to extreme value statistics so that we can extrapolate to 25-, 50-, or 100-year storms.
The next step, and one of the most difficult, is to evaluate the structure’s response to those extreme storms. The hydrodynamics of flexible structures are complex. And it is easy to significantly over-predict or under-predict structural requirements if you use overly simple estimates. So we need accurate, practical numerical modeling techniques for these structures. At Kelson Marine, we’ve worked with the U.S. Naval Academy, the University of New England, and Callentis Consulting to develop a Validated Tool for predicting Hydrodynamic Loads on large Macroalgae Farms, funded by our Department of Energy’s Advanced Research Projects Agency.
To develop a modeling tool for macroalgae farms, we:
- Measured the mechanical and geometric properties of real kelp species
- Built physical models of the kelp and tested them in a combined wave and tow tank.
- From that data, we derived hydrodynamic coefficients from which we construct what’s called a dynamic, finite-element model.
- What that means is we break every part of the farm—the kelp, the lines, the buoys—into small, finite elements, and at each instant in time the software tool solves for the forces on each element, and integrates those forces to compute the entire farm’s response to waves and currents.
We can then build finite element models of all kinds of farm designs and subject them to the maximum expected waves and currents for a particular site. We can predict things like the maximum tension in mooring lines, or how far below the surface the kelp sags down when the farm deforms. We can also design for operational considerations, like how much force it will take to raise a line to the surface for harvesting.
With this model in place, the biggest question for us as engineers was, does this tool give valid answers that can be used to design robust offshore farms?
So we deployed a farm at the University of New England’s site in Saco Bay, Maine, on the USA’s northeast coast. This site is fully exposed to the Atlantic ocean. The design conditions are a 1 m/s current and 4.2 m significant wave height.
Once the kelp was fully grown, we deployed load cells to measure the tensions in the mooring lines and simultaneously measured waves and currents. We collected data through a storm event, and the numerical model results for maximum tensions matched the measured tensions to within 15% RMS error. In other words, we demonstrated this technique to be sufficiently accurate to mitigate the risk of structural failure of moorings, attachments, and growth substrate.
We can now look for weak spots in the structure. We can analyze failure modes and effects and design to prevent cascading or catastrophic failure in the event of an accident.
The next question was, is this approach practical for informing wide ranges of design choices?
To evaluate that, we combined the dynamic model with a simple economic model for an example farm at our exposed site. The economic model included Capital expenditures, and approximated total biomass yield based on useable growline length and kelp growth as a function of average growline submergence. Using a design-of –experiments framework, we then quantified how various design choices such as line spacing, mooring scope, buoyancy, and mooring line stiffness affect the target metric–that is, biomass per dollar of capital expenditure.
And the surprising result was that when we examined the predicted biomass yield in kg per dollar of capital expenditure over the design space, we can see how sensitive the optimal design is to choices of line stiffness, mooring scope, and how much buoyancy is installed on the farm. These results suggest that a carefully-designed system can perform up to three times as well as our original design. And this is all done with simulations that can be run in a few days on a desktop computer. So we now have some confidence that this dynamic modeling approach is not only giving us valid results, but also has practical applications for designing novel offshore farms and optimizing for economic sustainability.
We have made great progress as an industry in being able to engineer successful offshore aquaculture structures. And I believe each one of these advances will take us a step further toward feeding the world and restoring our oceans in a way that is environmentally, socially, and economically sustainable.
Project Outcomes
Kelson Marine now has a method for efficiently predicting storm loads on open-ocean seaweed farms to within 15%, allowing us to engineer farm structures for maximum social, environmental, and economic sustainability.