
Seagriculture EU 2024: "Optimizing Seaweed Farming: Costs and Challenges"
Full Transcript
Offshore Wind and Aquaculture: Commonalities in the Engineering Supply Chain
Hey,
I’m Toby; an ocean engineer with Kelson Marine.
My “pitch” is that if you want to make money growing seaweed, you need to know what drives your long-term cost of production, and how to improve it.
At Kelson, we help design and test farms all around the world.
When I first started on seaweeds, I was focused on accuracy. It’s easy to overpredict the forces on a farm by 2- or 300%, or underpredict them, depending on what assumptions you use. But we were able to validate and calibrate our methods on full-scale farms in the ocean, thanks to ARPA-e MARINER and great partners like Ocean Rainforest. So then we focused on building these methods into an efficient design framework so that we can quickly answer questions like how well farms survive storms and prevent entanglement, or how flow speeds are distributed throughout the array, so that we can design structures that are robust and cost-effective.
And as we’ve done that, we’ve found there are design trade-offs that can only be resolved by calculating their impacts on the total cost of production. So…
… for the past few years, we’ve worked with the University of Maine, Woods Hole, and UNH to build a detailed, highly realistic techno-economic model, based on realistic farm designs and operational requirements for any site. This has allowed us to add the coupled interactions that have been missing from existing techno-economic studies.
We visually mapped all those interactions in the model, and the first 10% looks like this, so nevermind :)
But maybe most importantly, we’ve been able to validate this tool against some actual farm financials.
To share some of our findings from this research, I’ll use my favorite case-study that’s:
- 16 km from the US mainland.
- in 100m depth.
- With a Specific Exposure Energy of about 7 J/kg.
It’s a challenging site, but it was chosen for potential co-location with floating offshore wind.
Now this “specific exposure energy” is an index that synthesizes the complex interaction of waves, currents, and water depth into a single metric we can use for site selection and characterization.
And this past year we tested it by designing farms for 32 different sites in the North Sea and evaluating the loads on each one in that site’s 50-year storms. And we found this index is a much better predictor of structural requirements than other common metrics like distance from shore, water depth, or wave height.
(And that paper is submitted and there’s an online calculator for this index on our website. Now, we’re designing most of these farms to survive 50-year storms because that’s the return period prescribed in finfish standards. But we need to develop design guidelines that are specific to seaweed structures.
Just one example: We’ve started quantifying sites using return period contours, so we can show the actual probability of, for example, what wave height and current speeds can happen simultaneously. Existing standards prescribe combinations like 50-year wave height and 10-year current. But you can see that for this site, those combinations are well outside the contour of what combinations actually occur every 50 years. And this significantly impacts capital requirements. Other industries can afford that uncertainty; But seaweed cannot.
But now that we have a techno-economic tool that captures all these interactions and impacts, let’s look at what drives economics for this case study with:
- Annual harvest of Saccharina lattissima
- (with an integrated nursery operation)
- And a maximum allowable plot size of 40 hectares.
The first example finding from this research: We can quantify how cost of production changes with increased yield due to strain selection or other improvements:
Now, I decided to remove the actual cost-of-production numbers from these slides, because they need to be understood in the full context of this particular case. But they’re in the manuscript. So let me know if you’d like me to send you the pre-print.
But as your design yields increase, your capital and operational expenditures go up, and your revenue increases more, reducing cost-of-production. But there are diminishing returns with increased yield improvements.
One more example finding from this research: We get asked what scale is necessary to achieve financial viability. For this case, there are good economies of scale with today’s technologies up to about 120 hectares of permit area. But there are almost no gains beyond that without transformative mechanization and automation.
To summarize our findings:
For years, we’ve been showing sensitivity studies like this.
But when you accurately account for interactions—realistic farm designs for large, exposed sites, fuel costs with distance from port, the increased capital and operational expenditures associated with higher biomass--
The cost drivers and opportunities for achieving profitability are more like this:
- Yield matters; but it is not king.
- It is essential to optimize vessel costs,
- We need to significantly reduce structural costs per kg of biomass capacity, and
- we need to design farms for low maintenance,
- while improving yields.
…so that together we can build an industry that is economically sustainable.
Watch the Video
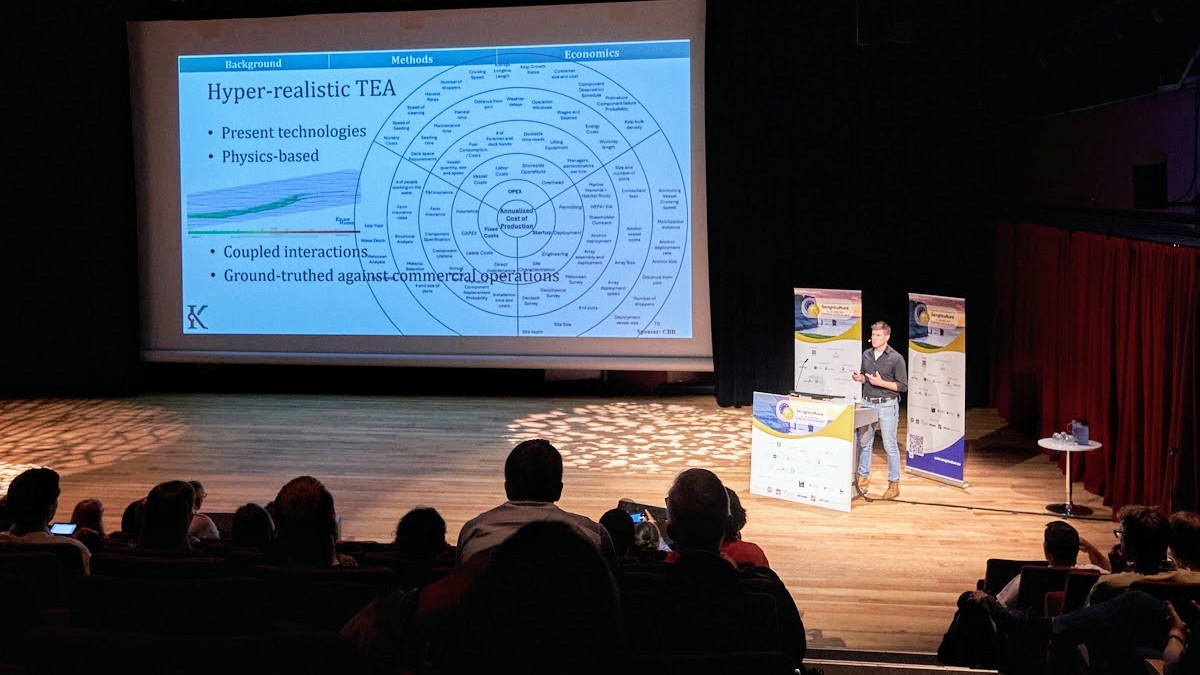